Industrial Hygiene Statistics & Core Components
Poor health costs employers 1.4 billion workdays of absence and $530 billion in revenue. Unfortunately, many organizations do not execute proper monitoring and standards to uphold the principles of industrial hygiene.
Industrial hygiene anticipates, identifies, and regulates potential or existing workplace environmental hazards. By preserving workplace health and safety, it maximizes workforce potential and fosters productivity. These industrial hygiene statistics illustrate the need for organizations to take a more proactive approach to health and safety.
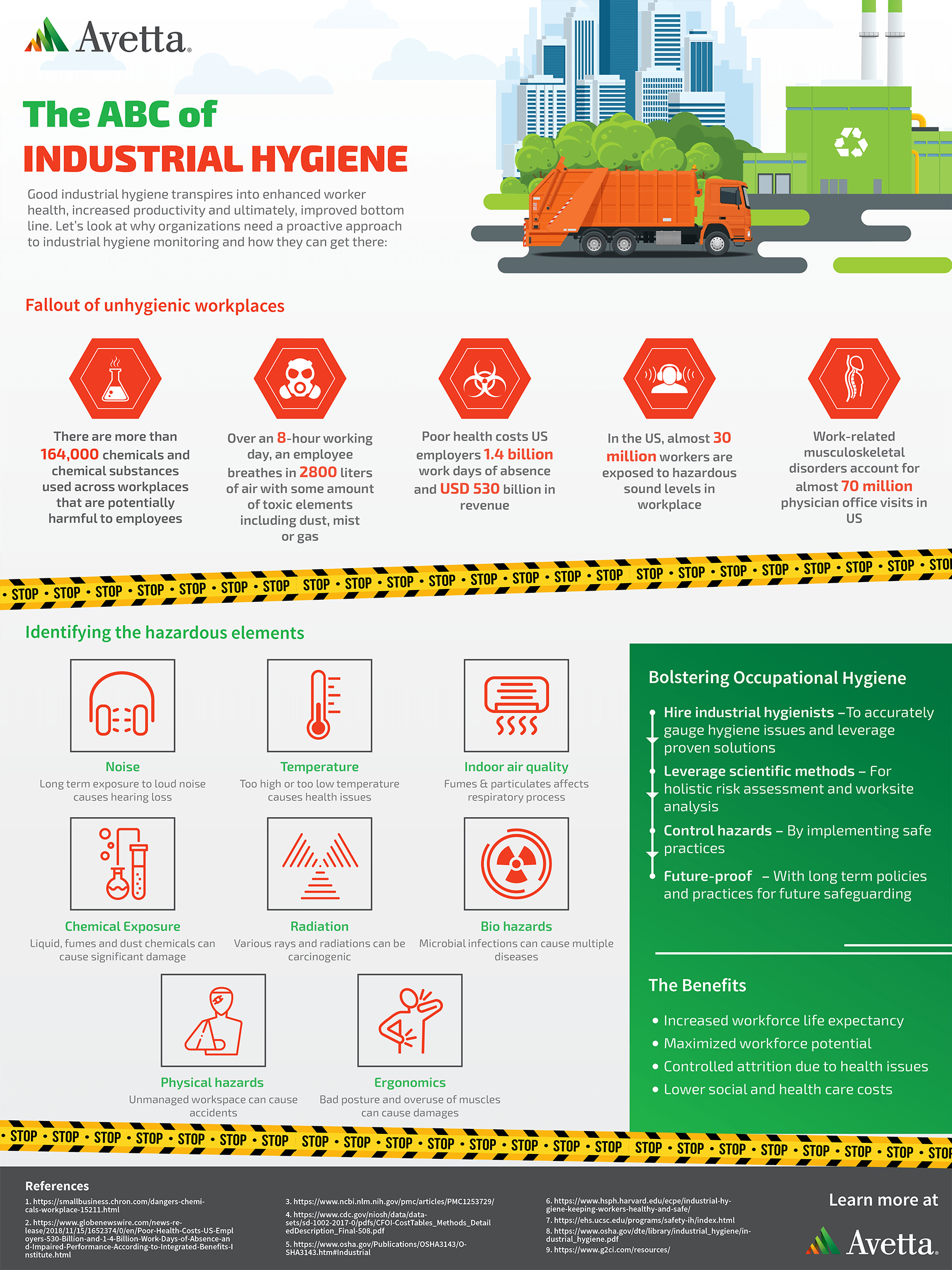
4 Core Elements of Industrial Hygiene
Safety is everyone’s concern. To effectively build a robust workplace grounded in occupational hygiene, organizations must understand the following core elements of industrial hygiene:
- Chemical - This includes gasses, fumes, dust, vapors, mists, and smoke that can pose dangerous health risks to employees.
- Physical - This includes extreme temperature, noise and vibration, and effects such as sunburn, hearing loss, or frostbite.
- Biological hazards - This includes agents and organisms such as bacteria, viruses, mold, and yeast that can cause illness and/or disease.
- Ergonomic - This includes physical positions and situations such as awkward postures, forceful exertion, and repetitive movements that cause bodily pain or injury.
Hazardous Elements in the Workplace
The health and safety hazards above cover a variety of stressors that can cause illness or extreme discomfort among employees. How exactly do these manifest in the workplace? Industrial hygiene can be broken down into eight hazardous elements:
1. Noise
Noise is one of the most prevalent occupational health problems in industrial and commercial work environments. Long-term exposure to loud noise can cause hearing loss and other health problems. Several staggering statistics illustrate why these issues persist:
- Almost 30 million workers are exposed to hazardous sound levels in the workplace.
- Thirty-four percent of workers exposed to noise do not wear hearing protectors.
- According to the same CDC findings above, 13 percent of workers exposed to noise have hearing impairment in both ears.
2. Temperature
According to the Occupational Safety and Health Administration (OSHA), millions of workers in the U.S. work in high temperatures, and thousands become sick from it. Risk factors of occupational heat exposure include:
- Heavy physical activity - This may be due to work in industries such as construction, agriculture, landscaping, etc.
- Warm or hot spaces - Workplaces such as bakeries, kitchens, boiler rooms, warehouses, etc. often produce high-temperature environments.
- Lack of acclimation - When employees are not provided sufficient time to build tolerance for higher temperatures, this can result in illness and even death. Per OSHA, 50 to 70 percent of outdoor fatalities occur within the first few days of working in high-temperature environments.
Exposure to cold temperatures can also bring health issues, such as frostbite, hypothermia, and trench foot. Those who work in outdoor professions like construction and recreational employees are most likely to be susceptible to cold stress.
3. Indoor Air Quality
The air quality of the indoor work environment plays a crucial role in the health, productivity, and comfort of employees. Over an eight-hour working day, an employee breathes in 2800 liters of air with some amount of toxic elements including dust, mist, or gas. These fumes and particulate matter can cause dizziness and nausea, along with respiratory issues such as asthma and chronic obstructive pulmonary disease (COPD).
4. Chemical Exposure
There are more than 164,000 chemicals and chemical substances used across workplaces that are potentially harmful to employees. Chemical exposure may cause serious accidents like fires and explosions, as well as both acute and chronic health issues such as skin irritation (burns and rashes), dizziness, heart ailments, and cancer.
- Approximately 32 million workers work with and are potentially exposed to chemical hazards.
- About 650,000 chemical products currently exist, and hundreds of new ones are presented annually.
5. Radiation
In workplace environments such as medical and dental offices and nuclear power plants, employees are exposed to ionizing radiation. The most common types of ionizing radiation are alpha and beta particles, gamma rays, and X-rays. These have enough energy to damage DNA and cause cancer if not properly controlled.
6. Biohazards
Biological substances such as microbial infections can pose a serious threat to workers’ health. These can include medical waste and samples of microorganisms, viruses, or toxins that may cause multiple infections and diseases. Biohazards are prevalent in industries like agriculture, sanitation, and healthcare. Approximately 320,000 workers die every year from exposure to biohazards in the workplace.
7. Physical Hazards
When workspaces are not properly managed and maintained, accidents can occur. Electrical hazards, along with slip, trip, and fall hazards such as broken stair rails, can bring serious injuries to workers. In 2016, 697 employees died from falls and 48,060 were severely injured and needed to take time off from work.
8. Ergonomics
As Americans spend over 2,000 hours in the workplace every year, ergonomics is critical in helping our bodies avoid musculoskeletal disorders (MSDs). MSDs, unfortunately, make up almost 70 million doctor office visits in the U.S. Repeated or forceful movements of the body can irritate and cause pressure around our nerves, producing conditions such as carpal tunnel syndrome and tendonitis.
4 Basic Principles of Industrial Hygiene
With several hazardous elements that can permeate the workplace, how can businesses efficiently combat these threats? Organizations should take a proactive approach by hiring industrial hygienists. With their help, organizations can effectively incorporate the four basic principles of industrial hygiene:
1. Ergonomics
What potential risks might arise that could put your employees in danger? Anticipation involves identifying possible threats before they are introduced. This may entail reviewing products, projects, and work environments. Through this, hygienists and organizations can begin designing regulations and programs specifically tailored to the business.
2. Recognition
What hazards are currently present? Identifying actual hazards before they cause harm provides organizations the opportunity to mitigate risk in the workplace. This might require looking into worksite and illness/injury analyses.
3. Evaluation
Monitor these potential hazards to determine the levels of exposure and illness. Data analysis, medical surveillance, and epidemiology can help make the right evaluations. For example, you may want to take air samples to check the indoor air quality and perform an exposure assessment to compare employees’ exposures to occupational exposure limits.
4.Control
With anticipating, recognizing, and evaluating, how do you control workplace hazards? Control requires eliminating processes or projects that pose high risks and administering necessary regulations. For example, companies can take action by:
- Establishing initiatives, such as a hearing conservation program. This program can provide provisions for noise measurement and measure noise exposure levels that convey the exact decibels employees are exposed to during an eight-hour shift.
- Providing protective equipment such as masks and earplugs to help protect workers from chemical and physical hazards.
- Building and streamlining requirements to ensure that all chemicals being used in the workplace are evaluated and information on the chemicals is thoroughly communicated to employees.
Human life should never be compromised. Bolstering occupation hygiene can increase workforce life expectancy, maximize workforce potential, control attrition due to health issues, and lower social and healthcare costs. Understanding relevant industrial hygiene facts can help organizations incorporate long-term policies and practices that will properly safeguard the future of their employees and business.